Technology DevelopmentProduction Engineering
JMU promotes the automation of production technology. One of our strengths is that we develop robots in-house. In addition to the welding robot applied to the assembly process of small blocks, we have recently developed a portable robot that can automatically recognize the welding points. This makes it possible to automate confined and narrow areas where it was difficult to be welded by robot.
We also utilize ICT and IoT to realize digital transformation (DX) at shipbuilding sites. In focusing on the development of monitoring technology at shipbuilding sites, the collected daily big data from hundreds of welding machines improve the efficiency of welding work. Visualized company-wide date enable to control accuracy and equipment maintenance.
3D Job-order system
Manufacturing assist system for easy understanding of the Work Procedure
This system provides production workers graphical job-orders on the screen of mobile PC’s or slate-type PC’s. The job-orders give hull structure workers assembly sequence of 3D structure blocks or outfitting workers fitting orders of 3D outfitting pieces together with proper dimension lines and some notations. We are aiming at so-called paper-less production.
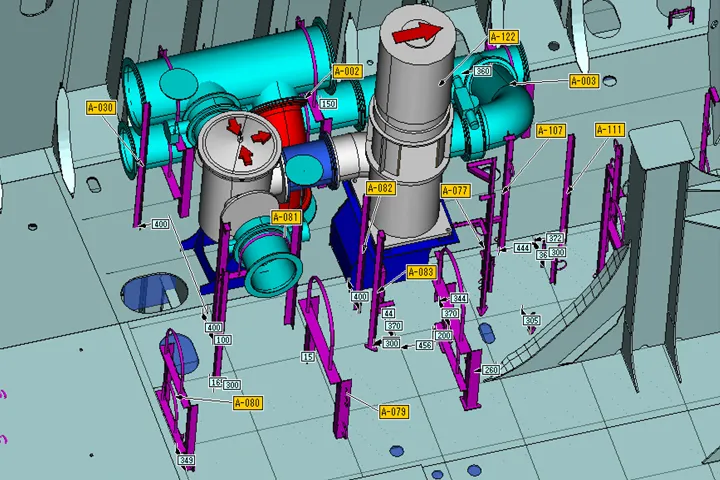
Welding robot
Welding robot system for sub-assembly
This production system consists of four traveling girder equipped with twin robots, and operation data are generated by our original CAD/CAM system. This system has achieved efficient productivity by interference check between multiple robots, and also can generate optimal operation data.
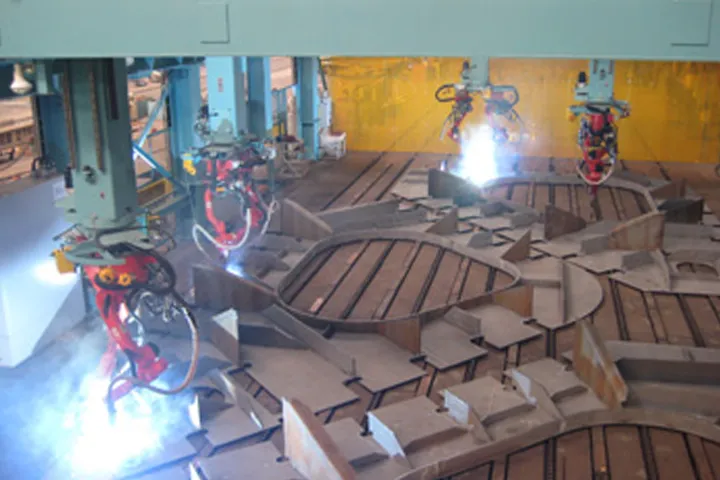
Welding robot system for hull block assembly
This production system consists of 16 welding robots, and operation data are generated by our originally developed CAM system. This robot system has contributed to the improvement of welding quality and productivity by gap adaptive control and function of welding of curved joints.
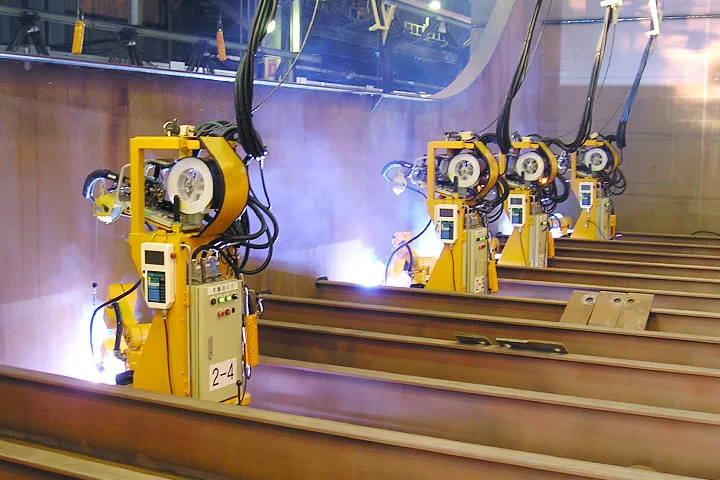